The Delicate Balance of Strength and Emotion Transforms Rugged Metalinto Beautiful Curves
Craftsman Dialogue 01
The metal spinning
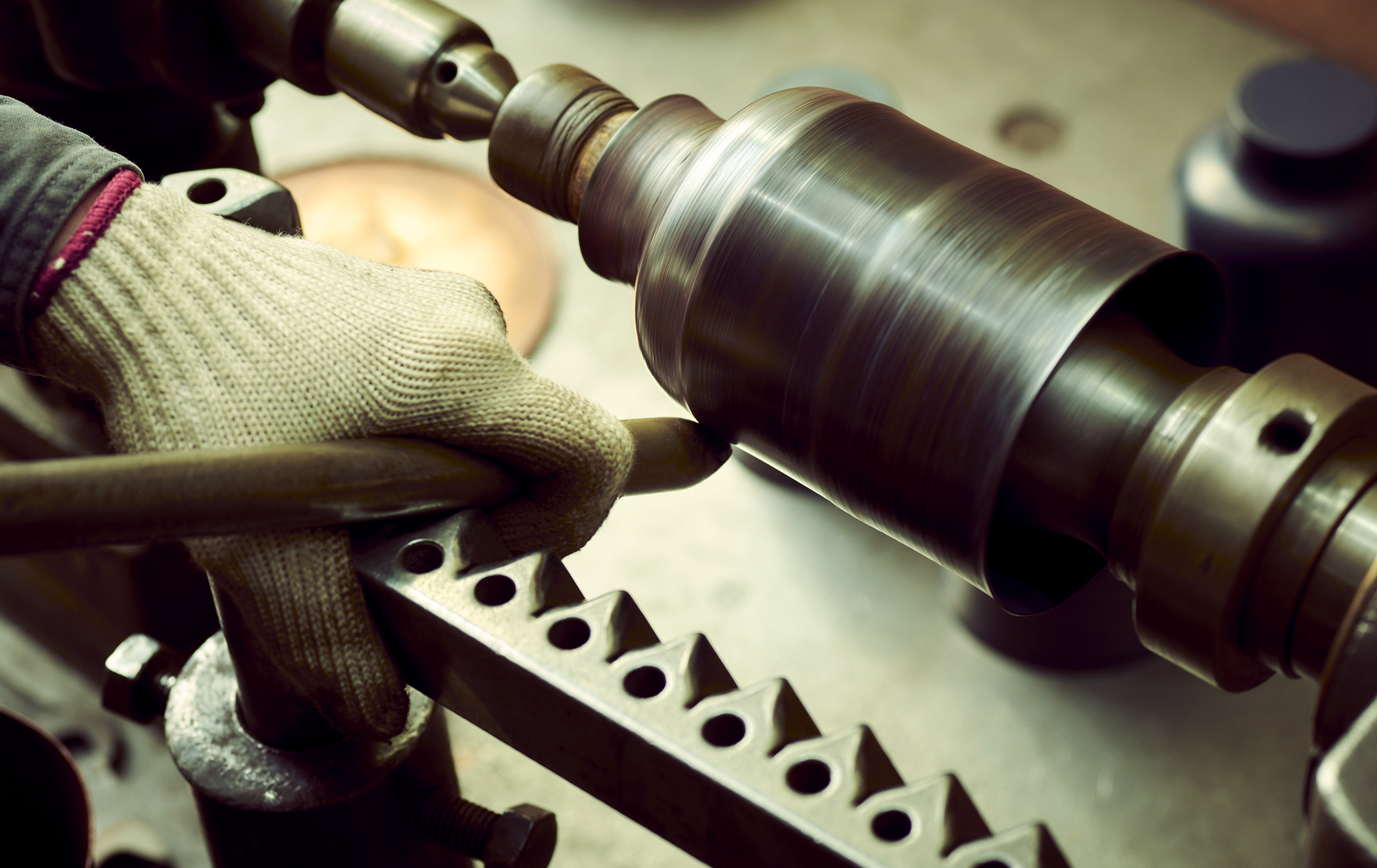
The base material for cloisonne is a single sheet of pure copper. The metal spinning (Hera-shibori) process involves stretching the copper sheet over a rotating mold to shape it into vases and vessels.
Skillfully adjusting pressure with a spatula is a defining aspect of metal spinning and ensures uniform thickness while crafting curves. The technique condenses the essence of the material into its final form in a matter of hours. Now, efforts are ongoing to connect with the next generation and pave the way for the future.
Pressing, Stretching, Firing: Every Task Demands Masterful Skill
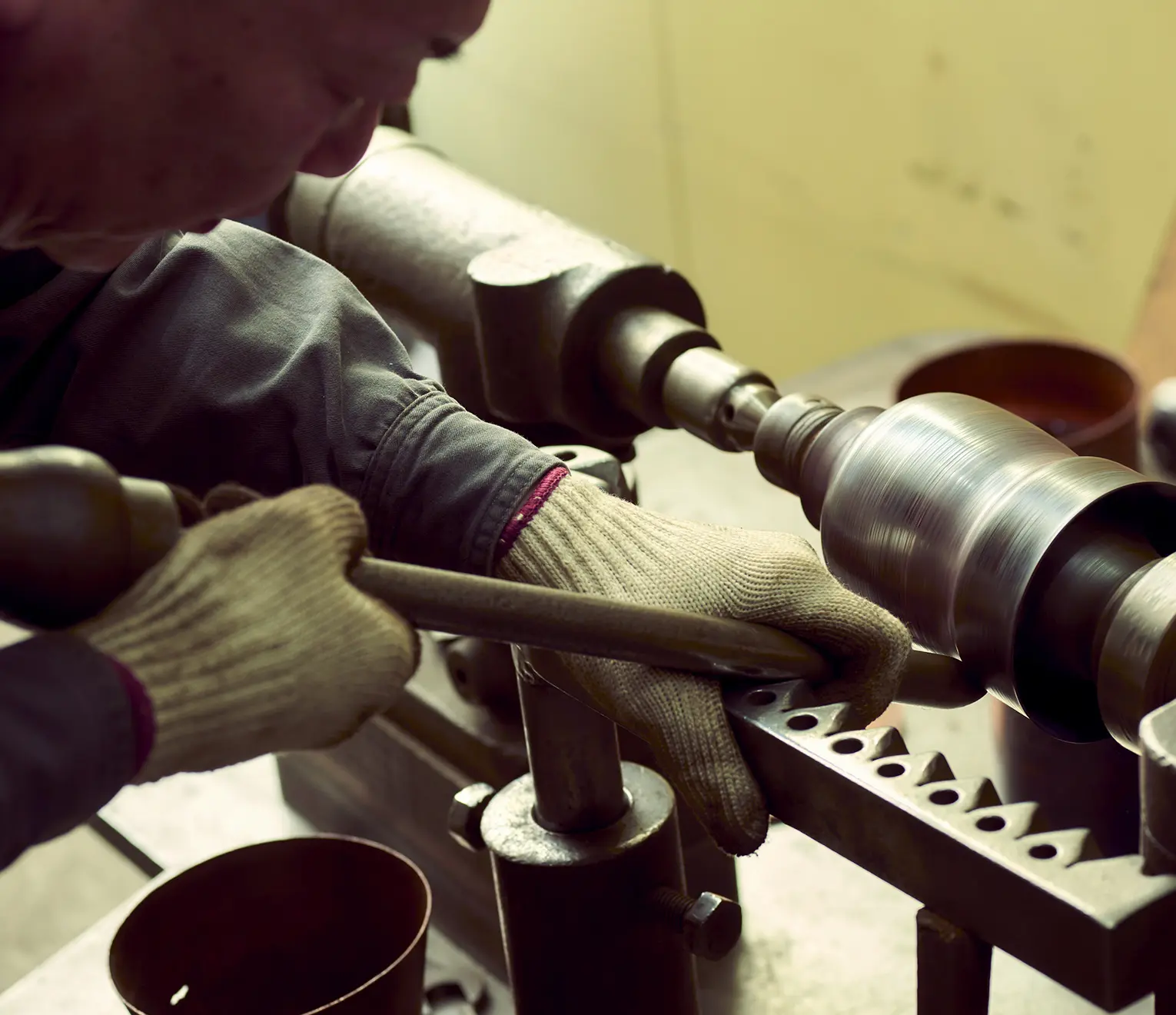
A machine known as a spinning lathe secures the metal mold, clamping a circularly cut sheet of copper in place. Once the lathe starts rotating, a metal spoon (Hera-bo) is leveraged against the copper— similar to shaping pottery on a wheel, the flat copper sheet swiftly takes on a curved form, transforming into the shape of a vase.
"I've been in this profession since I left school, as my family business was metal spinning," says Nishiura, a craftsman with over 40 years of experience in metal spinning. Although he once ran his own metal spinning workshop, he joined forces with Ando Cloisonne at their request, eager to pass on his skills. "I might be the only one left in this area known as a metal spinning artisan," he remarks, indicating that this technique is a rare skill mastered by only a few.
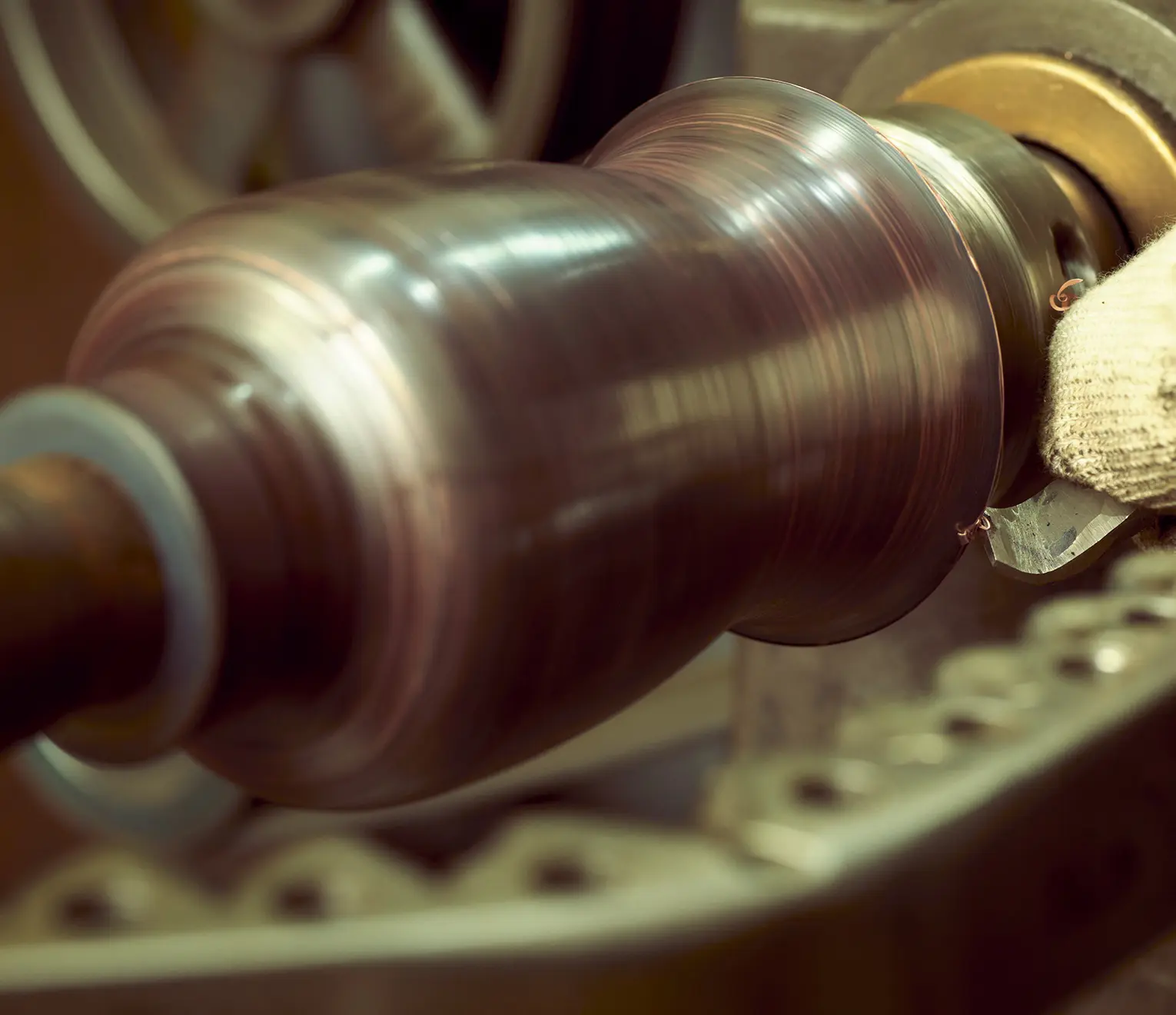
The most technically demanding aspect of metal spinning is the application of force. Just as hammering metal with a mallet can create uneven thick and thin areas, incorrect pressure application with the metal spoon can result in uneven thickness and surface irregularities on the shaped substrate. Metal spinning artisans use their entire body to adjust the force applied, ensuring consistent thickness throughout the piece.
During the metal spinning process, the workpiece undergoes several rounds of annealing. Annealing involves placing the shaped metal into a kiln to heat it, which relieves stress and makes the metal more malleable for further shaping. "If you overheat it, the surface becomes rough, so I watch the color of the copper to time it perfectly," says Nishiura. The annealing time varies subtly depending on the size and shape of the substrate, making this another step where the artisan's experience and intuition are crucial.
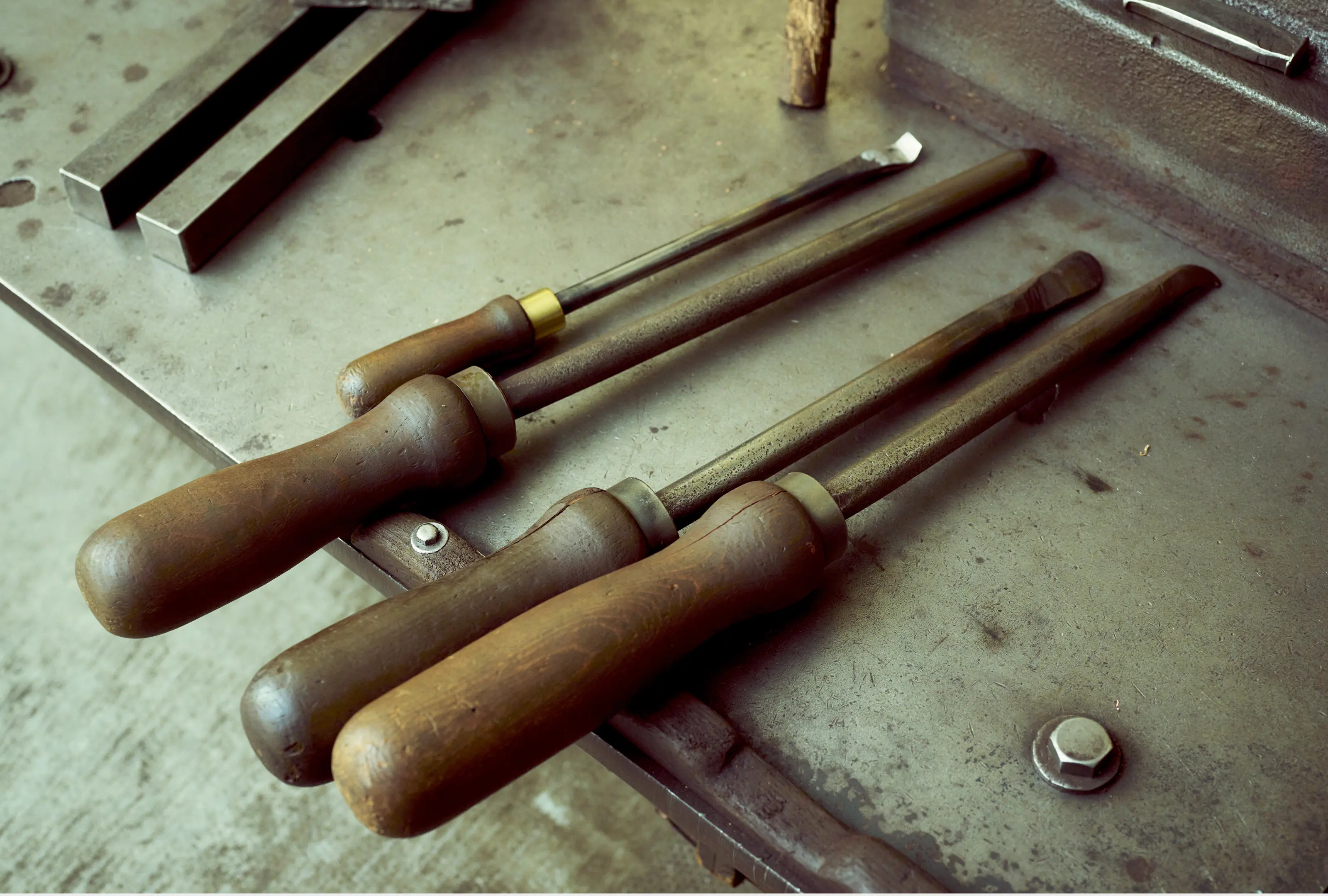
If There's No Mold, Make It Yourself: Even Woodworking Is the Craftsman's Task
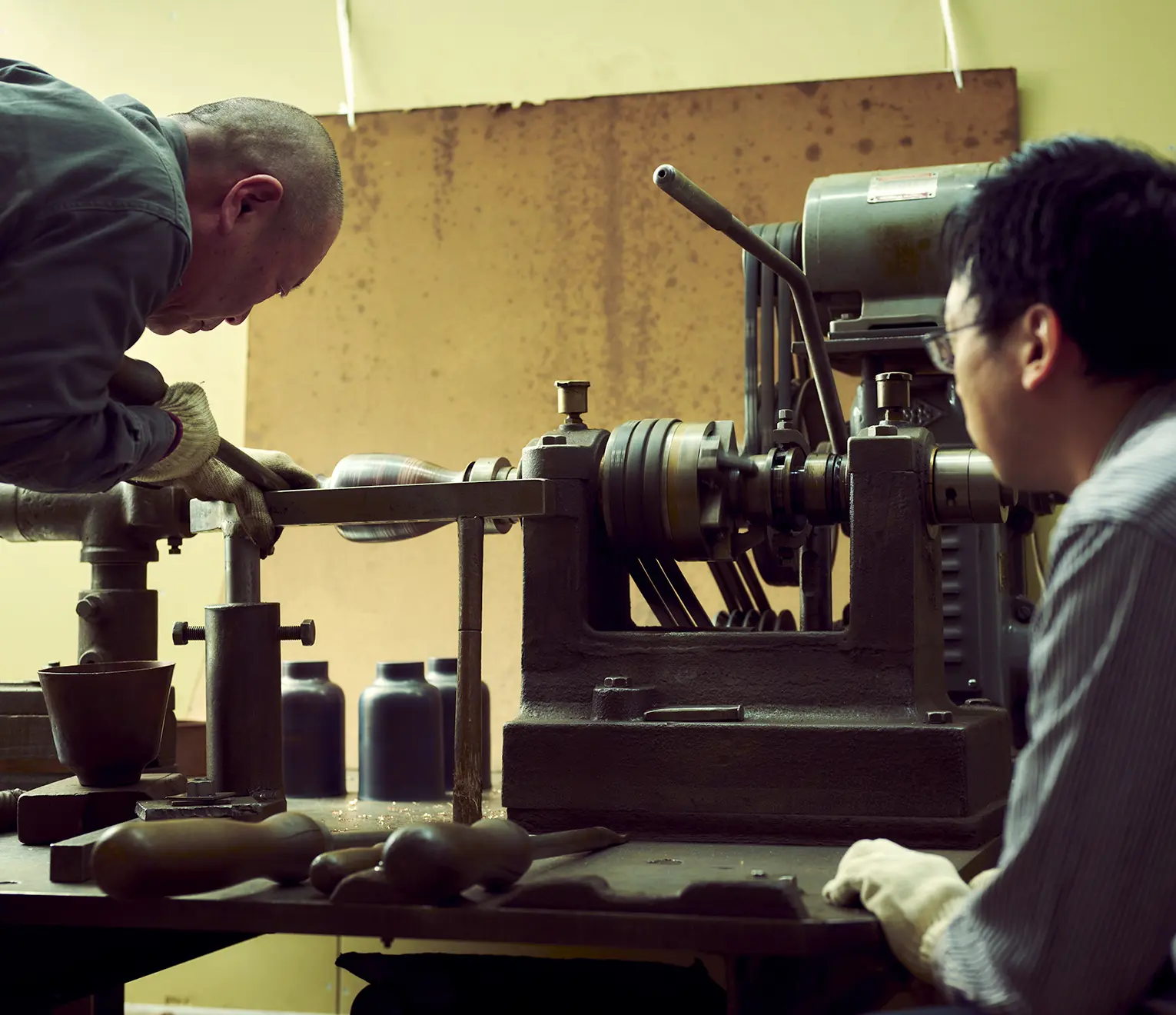
Hiroi watches as Nishiura skillfully performs metal spinning on a copper plate. Hiroi joined Ando Cloisonne at the age of 18 and has spent 20 years honing his skills, mainly in wiring and polishing. Aiming to inherit the specialized role of metal spinning, a task only a few can undertake, Hiroi has been building his career in this process under Nishiura's guidance. Reflecting on his initial foray into metal spinning, Hiroi recalls, "I couldn't grasp the right amount of force to use, and I was in constant pain from the physical effort." Now, after about three years, he increasingly handles the process on his own.
Yet, he admires his mentor, noting, "Even when shaping the same substrate, Mr. Nishiura uses fewer pushes with the metal spoon. He also completes the work more quickly." Nishiura responds, "The environment I grew up in was all about producing in quantity. I want the younger generation to take their time and try different things, even if it takes longer at first."
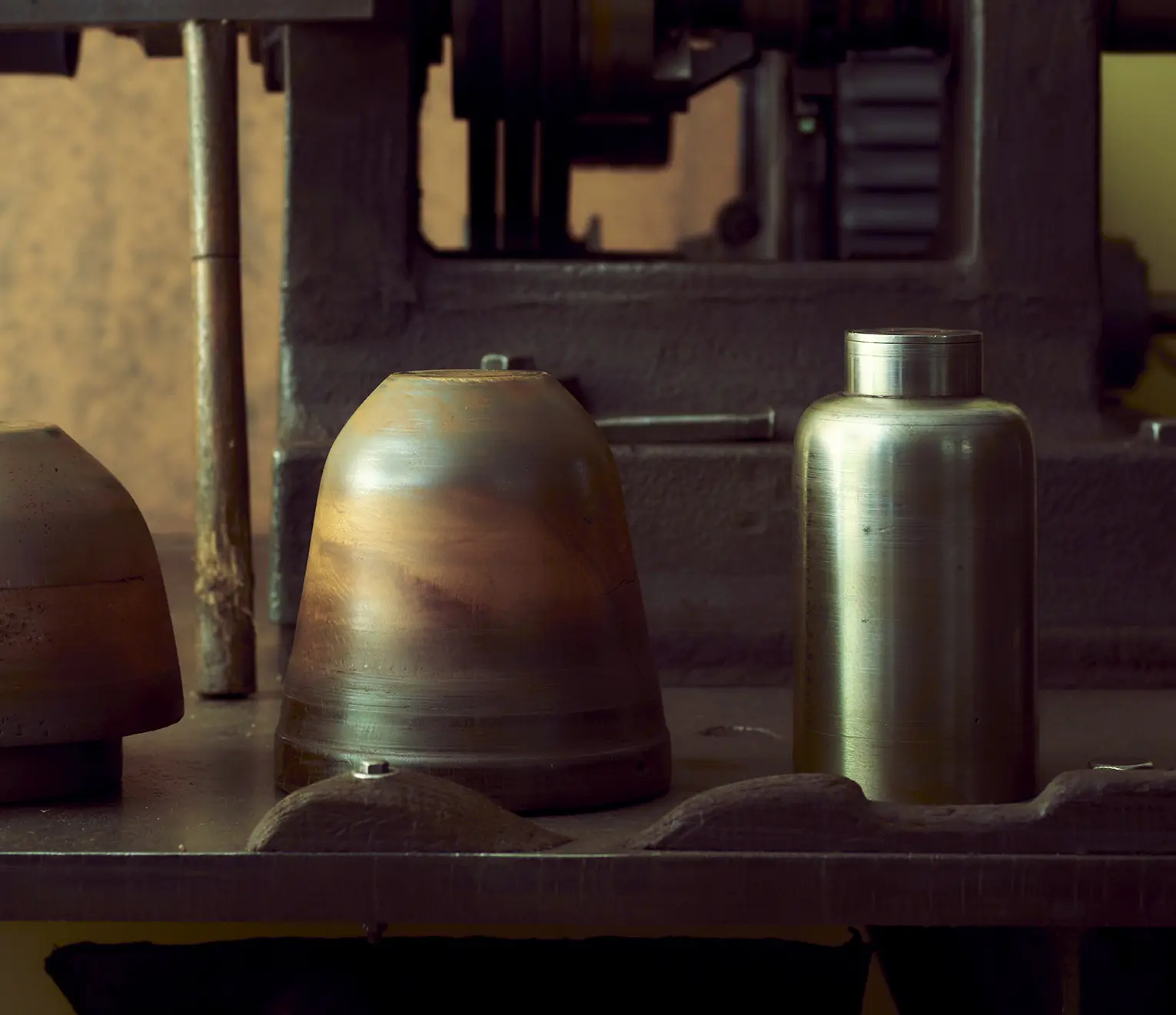
Molds used in metal spinning are typically made of metal for off-the-shelf products, but custom orders require creating molds from scratch. Mold-making is another crucial process undertaken by metal spinners. They use magnolia, a deciduous hardwood from the Magnoliaceae family, and carve it out using chisels and other tools. "I expand the three-dimensional image in my mind while looking at the drawings and then carve it out in one go" says Nishiura. Ando Cloisonne is known for its original cloisonne designs, such as the Takamatsu-no-Miya Cup, but it’s often the manual work of metal spinning artisans that marks the starting point for these unique pieces.
"My father, who spent about 70 years in metal spinning, was incredibly fast at carving wood molds. I'm still far from matching his speed, but I aspire to catch up," Nishiura shares, reflecting on the example set by his father. The skills that the master continues to hone will eventually be passed down to Hiroi.
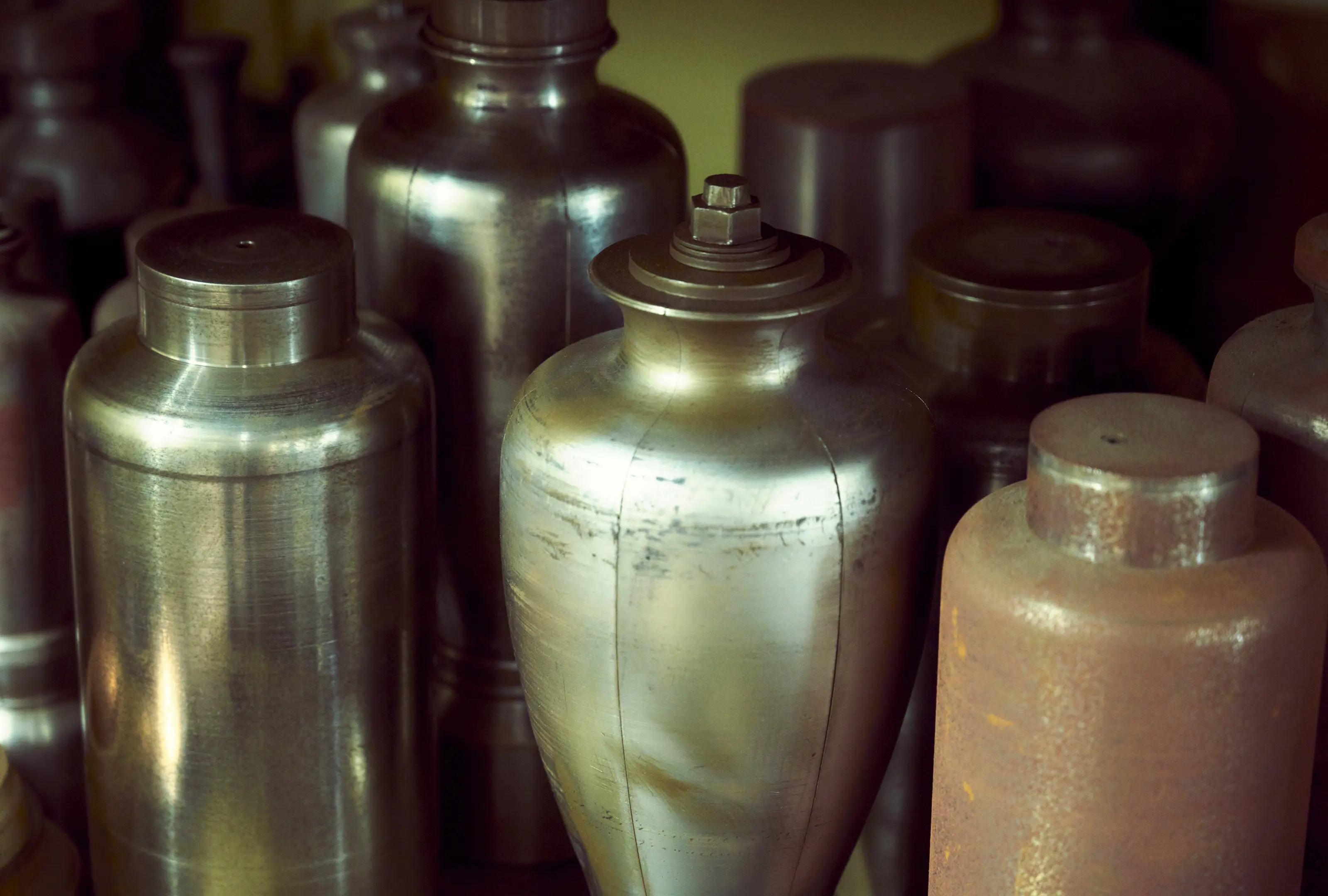
The Future of These Seemingly Colorless Processes Shines in Various Hues
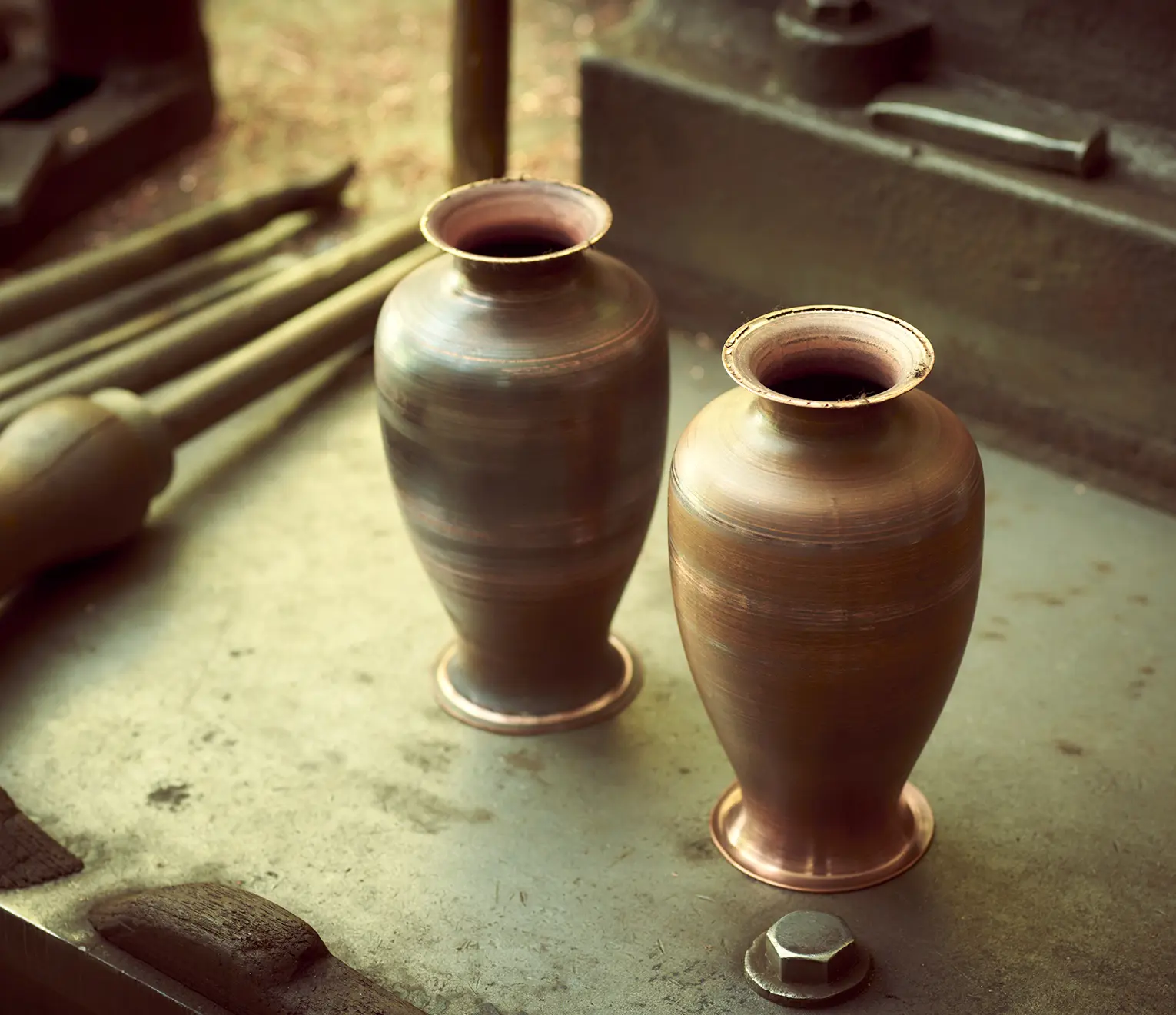
Metal spinning artisans are required to shape products to the desired quality and quantity in a short amount of time according to orders. While press forming—applying pressure with machines—has the advantage in mass production, metal spinning can be quicker for certain lot sizes, and without leaving any processing marks, it allows for a more beautiful finish. Most importantly, as Nishiura says, "The charm of cloisonne lies in its high degree of freedom," making it an essential process for creating unique masterpieces, and this joy becomes the driving force for metal spinning artisans.
Nishiura continues, "Ando Cloisonne has come this far by preserving the artisans and their techniques, maintaining high quality, and ensuring customer satisfaction. Even with processes other manufacturers have given up on, we have the confidence to accomplish them."
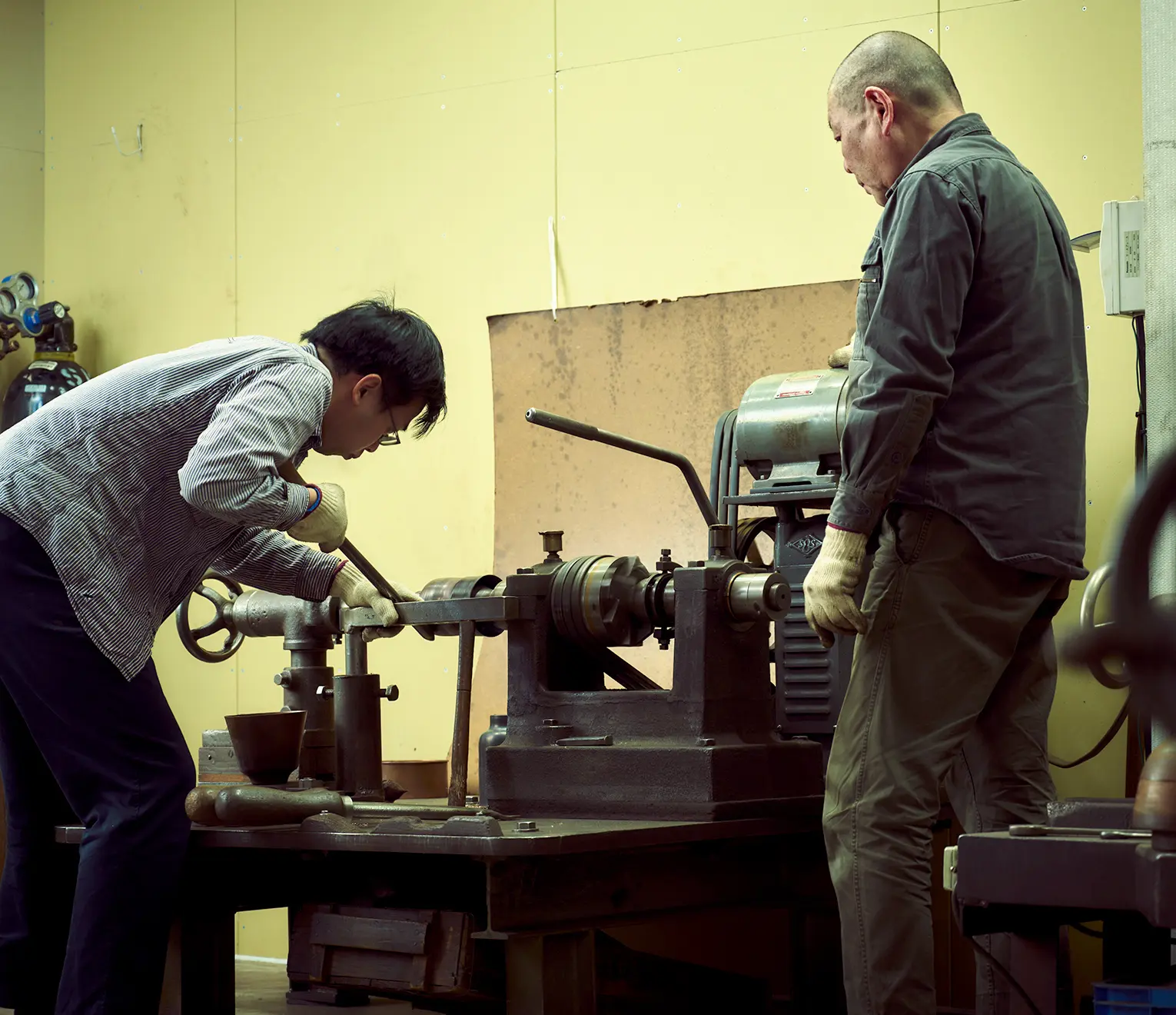
Hiroi, the inheritor of the technique, envisions the same future as Nishiura. "Creating a cloisonne globe was a memorable experience. It was challenging to shape a large sphere with Mr. Nishiura, but it was also very rewarding. I want to continue to take on custom orders that utilize metal spinning techniques, raising the profile of both Ando Cloisonne and the art of cloisonne itself," he says with a bright expression.
In the art of cloisonne, known for its translucent colors, the metal spinning process might seem "colorless" to an onlooker. However, it's a vital step that underpins the beauty of cloisonne, and the future of the craftsmen who support it shines brightly in various colors.
-
Craftsman Dialogue 02
Expanding the Possibilities of Cloisonne with Pioneering and Innovative Techniques
-
Craftsman Dialogue 03
Anticipating Completion, Standing Silver Wires: A Craft Nurtured by Skill and Experience
-
Craftsman Dialogue 04
Clad in Vivid Colors, Infused with Soul: Crafting Beauty that Resonates